Vacuum Forming
Vacuum forming uses the atmospheric air pressure to form plastic sheet that has been heated to its designated forming temperature. The plastic sheet is placed over the shape to be formed and an air tight seal is achieved around the perimeter of the part. The air beneath is then evacuated from the tool. This causes the plastic sheet to form to the shape that is required by the weight of the atmosphere.
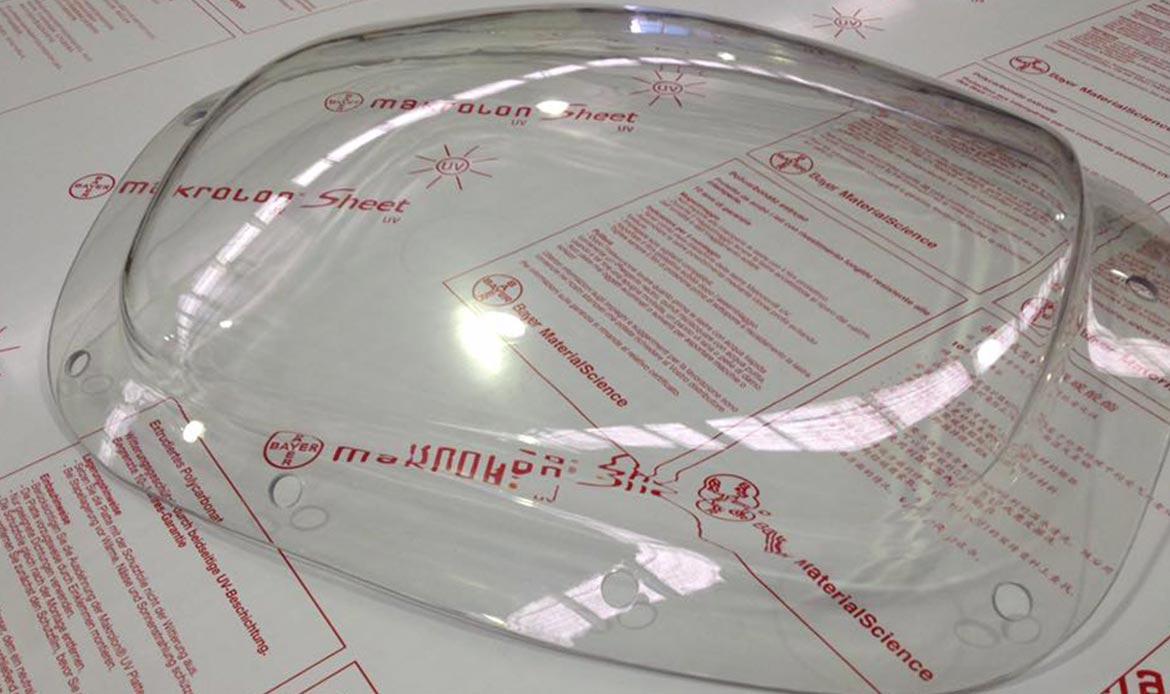
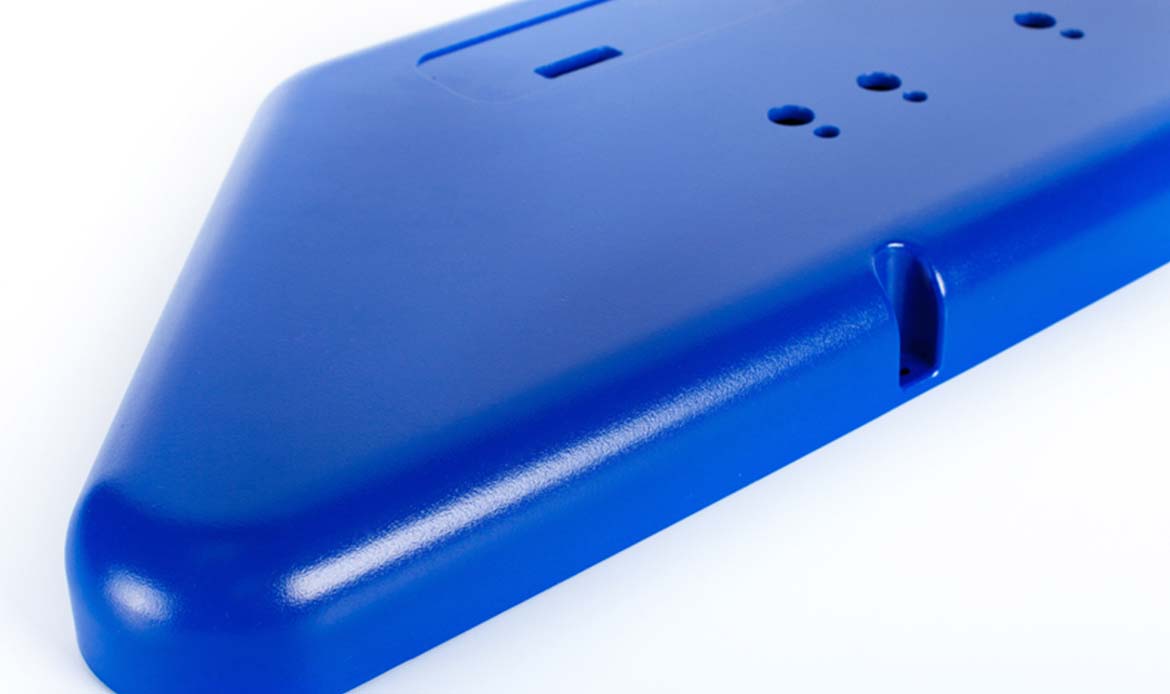
Pressure Forming
Pressure forming can be described as advanced vacuum forming. Using higher air pressure to achieve better definition on the part. To achieve this, tooling costs are much higher and complicated. Aluminium castings are normally used to take the higher pressures and cooling pipes need to be imbedded to keep the tool temperatures stable. Health and safety issues plus capacity of equipment need to be taken into account.
Free Forming
Free forming is probably the first way of shaping plastic sheet but instead of using a vacuum, using air pressure. Going back to the 1930’s when the first acrylic material was being developed. Clear acrylic was a much lighter material than glass and could greatly reduce weight in an aircraft but how to get rid of the distortion when forming. The answer was to use air to blow the part to the required shape.
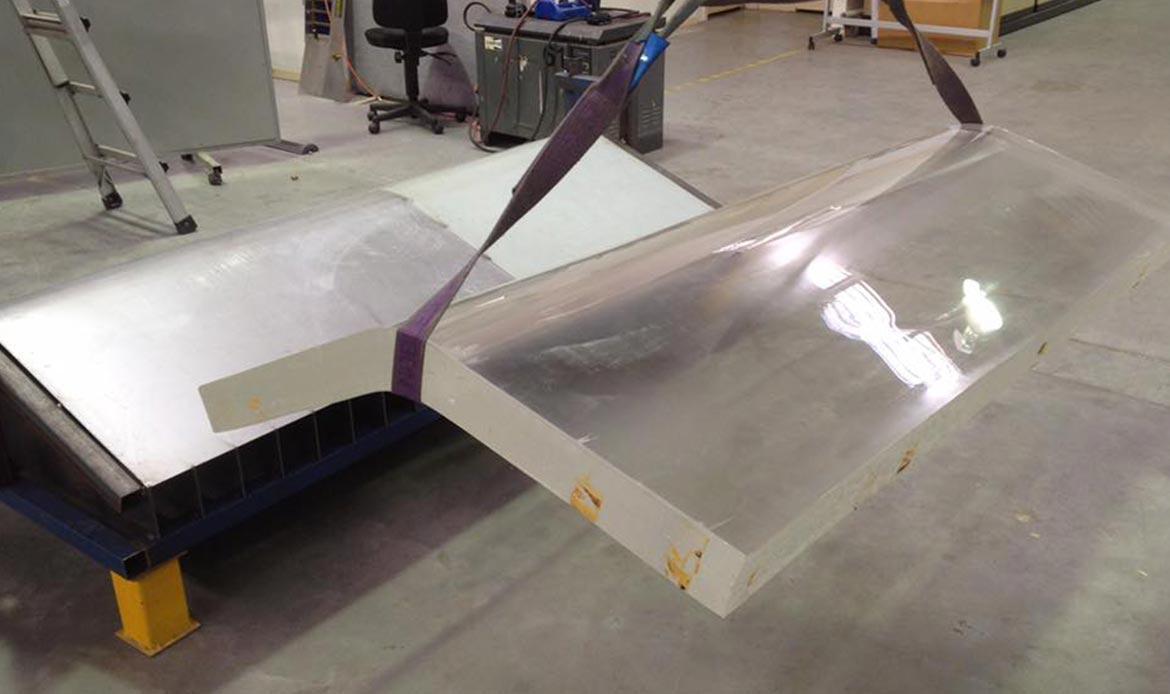
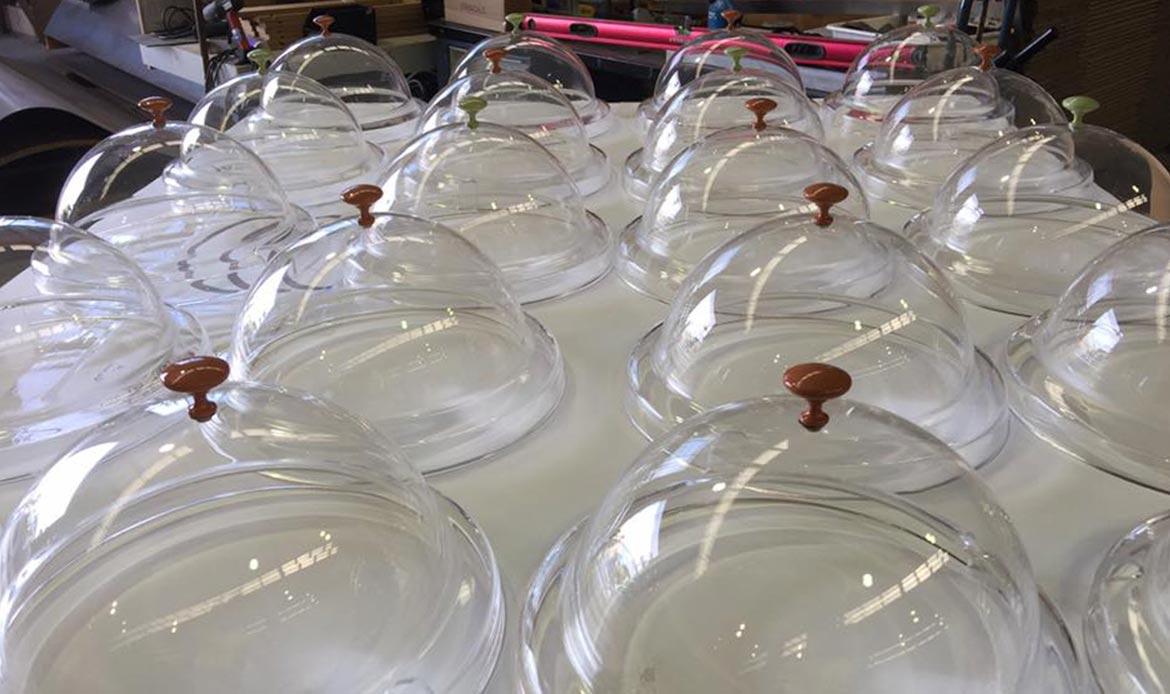
Polycarbonate Moulding
Polycarbonate plastic forming presented a new challenge for the plastics industry. A high tech material with incredible strength and a high temperature performance. The advantages were there but the processing was entirely different. New thinking and equipment was required. Atlas invested in new and more advanced machinery and became the best known name in formed polycarbonate parts with optical performance.